In the intricate world of machining, thin-wall milling stands as a testament to the marriage of precision and complexity. Crafting components with delicate, thin walls is a common requirement in industries such as aerospace, automotive, and medical device manufacturing. However, the process is fraught with challenges, with deformation being one of the most significant hurdles to overcome. This blog post delves into the best practices for minimizing deformation in thin-wall milling, enabling you to achieve high-precision results consistently.
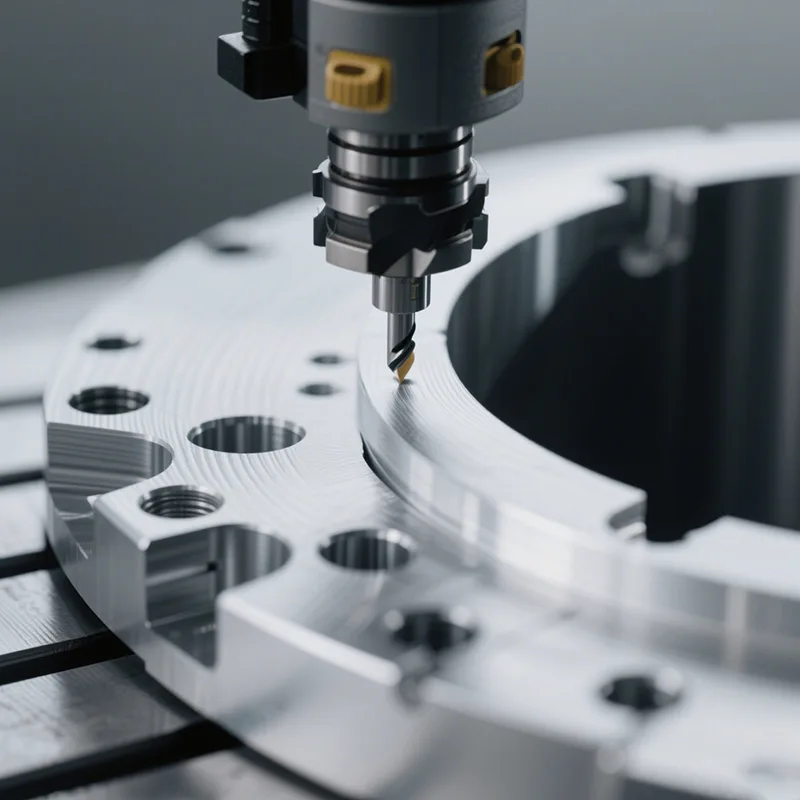
Understanding the Causes of Deformation in Thin-Wall Milling
Before exploring the solutions, it's crucial to understand what causes deformation in thin-wall milling. Several factors contribute to this issue:
- •Cutting Forces: The forces generated during the milling process can cause the thin walls to flex and deform. High cutting forces, especially in large-depth cuts, exacerbate this problem.
- •Heat Generation: Friction between the cutting tool and the workpiece generates heat, which can cause thermal expansion and subsequent deformation of the thin walls.
- •Vibration: Uncontrolled vibrations during machining can lead to inconsistent cutting and cause the thin walls to vibrate and deform.
- •Workpiece Material Properties: The material's properties, such as its strength, stiffness, and thermal conductivity, can influence its susceptibility to deformation.
Best Practices for Minimizing Deformation
- 1. Optimize the Cutting Parameters
-
Adjusting the cutting parameters is a fundamental step in minimizing deformation. Here are some key considerations:
- •Spindle Speed: Increase the spindle speed to reduce the cutting forces. Higher spindle speeds result in smaller chip loads, which helps to minimize the deflection of the thin walls.
- •Feed Rate: Decrease the feed rate to control the cutting forces and prevent excessive material removal. A slower feed rate allows for better chip evacuation and reduces the risk of tool breakage.
- •Depth of Cut: Use a smaller depth of cut to reduce the cutting forces and minimize the deflection of the thin walls. Multiple passes with a smaller depth of cut are often more effective than a single deep cut.
- •Axial and Radial Chip Thickness: Optimize the axial and radial chip thickness to balance the cutting forces and minimize the deformation of the thin walls.
- 2. Select the Right Cutting Tool
-
The choice of cutting tool can significantly impact the deformation in thin-wall milling. Consider the following factors when selecting a cutting tool:
- •Tool Geometry: Choose a cutting tool with a sharp edge and a small nose radius to reduce the cutting forces and improve the surface finish. A tool with a variable helix angle can also help to reduce vibration.
- •Tool Material: Select a cutting tool made from a high-performance material, such as carbide or ceramic, to withstand the high cutting forces and temperatures generated during thin-wall milling.
- •Tool Length: Use a shorter tool length to reduce the overhang and minimize the deflection of the cutting tool. A shorter tool also provides better stability and control during machining.
- 3. Implement Proper Workholding Techniques
-
Effective workholding is essential for minimizing deformation in thin-wall milling. Here are some workholding techniques to consider:
- Vacuum Chucks: Vacuum chucks provide a secure and uniform clamping force, which helps to prevent deformation of the thin walls. They are particularly useful for holding delicate workpieces.
- Magnetic Chucks: Magnetic chucks offer a quick and easy way to hold ferrous workpieces. They provide a strong clamping force and can be adjusted to accommodate different workpiece sizes and shapes.
- Mechanical Clamps: Mechanical clamps, such as vises and clamps, can be used to hold workpieces securely. However, care must be taken to ensure that the clamping forces are evenly distributed to prevent deformation of the thin walls.
- Support Structures: Use support structures, such as backers and fixtures, to provide additional support to the thin walls during machining. This helps to reduce the deflection of the thin walls and improve the machining accuracy.
- 4. Control the Machining Environment
-
Controlling the machining environment can also help to minimize deformation in thin-wall milling. Here are some factors to consider:
- •Coolant and Lubrication: Use an appropriate coolant and lubrication system to reduce the cutting forces and temperatures generated during machining. Coolant helps to flush away the chips and keep the cutting tool and workpiece cool, which reduces the risk of thermal deformation.
- •Machine Vibration: Minimize machine vibration by ensuring that the machine is properly maintained and calibrated. Use vibration-damping mounts and fixtures to reduce the transmission of vibration to the workpiece.
- •Ambient Temperature and Humidity: Control the ambient temperature and humidity in the machining environment to minimize the thermal expansion and contraction of the workpiece. This helps to maintain the dimensional accuracy of the thin walls.
- 5. Employ Advanced Machining Strategies
-
Advanced machining strategies can also be used to minimize deformation in thin-wall milling. Here are some strategies to consider:
- •Adaptive Machining: Adaptive machining uses real-time feedback from sensors to adjust the cutting parameters during machining. This helps to optimize the machining process and minimize the deformation of the thin walls.
- •High-Speed Machining: High-speed machining involves using high spindle speeds and feed rates to reduce the cutting forces and improve the surface finish. This strategy is particularly effective for machining thin walls made from difficult-to-machine materials.
- •Multi-Axis Machining: Multi-axis machining allows for more complex toolpaths and better access to the thin walls. This helps to reduce the cutting forces and minimize the deformation of the thin walls.
Conclusion
Minimizing deformation in thin-wall milling is a critical challenge in the machining industry. By understanding the causes of deformation and implementing the best practices outlined in this blog post, you can achieve high-precision results consistently. Remember to optimize the cutting parameters, select the right cutting tool, implement proper workholding techniques, control the machining environment, and employ advanced machining strategies. With these strategies in place, you can overcome the challenges of thin-wall milling and produce components with the highest level of precision and quality.
If you have any questions or need further assistance with thin-wall milling, please feel free to contact us. We are here to help you achieve your machining goals and ensure the success of your projects.